Featured in this post
Choosing the Right Food Traceability Software: Features That Matter Most
Choosing the Right Food Traceability Software: Features That Matter Most
15 Jul 2025
John McCurdy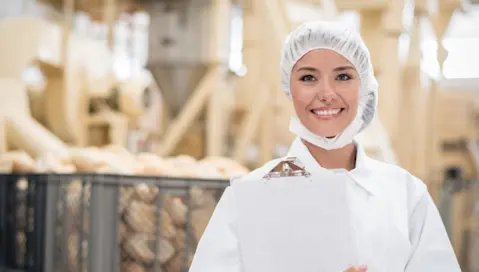
Each year, the United States sees approximately 800 foodborne illness outbreaks, resulting in 15,000 illnesses, 800 hospitalizations and 20 deaths. These are powerful reminders that even a single misstep in food safety can have far-reaching consequences.
That’s why your food product traceability procedures can’t afford to be built on spreadsheets, sticky notes or someone’s memory. Manual methods not only slow your operations down, they also leave room for costly mistakes—missed lot numbers, mislabeled products or delayed responses when speed matters most. And let’s not forget the paper clutter, inconsistent documentation and time your employees lose chasing down data instead of focusing on production.
In contrast, purpose-built traceability software provides organization, standardization and confidence that you’re set up for success. Implementing an industry-specific food ERP is one of the most effective ways to tackle your food traceability challenges head-on—offering every tool and feature your team needs to track ingredients, sublots, packaging, labeling, shipping and more. It eliminates the inefficiencies of manual tracking across your supply chain and reduces the risk of human error. This helps you ensure greater accuracy—crucial when transparency for consumers and public health is on the line.
This blog walks you through the specialized features you’ll find in the best food traceability software, how they work and why they’re essential for food safety, quality control and peace of mind. Because the better your system, the fewer surprises you—and your customers—have to deal with.
1. Lot Management
Full traceability requires end-to-end supply chain visibility, and in the food and beverage world that means lot tracking with coverage down to sublots and individual items. The lot management features of food ERP systems enable you to follow your goods and their associated traceability data from raw material to finished item. This means you know exactly where each ingredient came from, when it was processed and where it ended up. This level of traceability is essential for food safety, efficient product recalls and accurate audit trails.
Plus, when shelf life and expiry are at stake, you need a system that can keep up. With automatic alerts and easy visibility into lot details, you can act quickly when something’s off instead of scrambling when it’s too late. The right solution also gives you sublot management features so you can drill down even further—think harvest batches, partial repacks or multi-step processing events. That extra granularity gives your team better control over inventory and quality, especially when lots are split, blended or reworked. No more referring to paper traceability records or re-entering traceability data. The result? Stronger food safety, airtight compliance and a smoother workflow for your team on the floor.
2. Advanced Attributes
The advanced attribute capabilities of a leading food ERP go far beyond static data fields. They let you assign custom product characteristics—like country of origin, allergen content or ideal storage conditions—so your traceability system reflects real-world complexity. That means fewer gaps in documentation, minimal errors and better consistency in how your employees handle and report data. Even better, this level of visibility facilitates all critical food safety functions like regulatory compliance, allergen management and contamination prevention. In other words, it gives your team the clarity and context they need to act as fast as possible when safety is at stake.
With these features, you can group products or lots by specific traits, track how they move through your supply chain and segment information to surface exactly what you’re looking for. Say you need to pull up all products from a certain vendor or identify the allergens in specific items—filters and searchable attributes make that a breeze. Since this information appears directly in your system’s list pages and dashboards, your team can quickly isolate any contaminations, follow correct put-away procedures and verify that packaging and labeling include all required ingredient declarations. That gives you and your consumers a greater degree of confidence that your food is compliant, handled with utmost care and labeled accurately.
3. License Plating and SSCC
License plating is critical for tracking products in busy food and beverage facilities. A food and beverage ERP system allows you generate new license plates for pallets, cases or mixed lots—and/or scan and record ones already applied by suppliers using barcode technology. This flexibility supports both inbound and outbound operations, reduces manual entry and ensures consistent tracking across your facility. Since these industry-standard identifiers are retained throughout the supply chain, you gain end-to-end visibility that minimizes errors, facilitates transactions and improves overall warehouse efficiency.
Similarly, food industry-specific ERP systems support the handling of serial shipping container codes (SSCCs), which are crucial for traceability during transport. Whether your team is creating SSCCs in-house or logging those provided by a logistics partner, your ERP can accommodate both. Built-in features such as guided code assignment, label printing and customer-specific validation checks simplify the process and ensure compliance.
You can also configure and assign custom labels for customers, vendors and items using ERP templates. With each SSCC tied to a complete shipment history—including contents and movement—you’re always prepared for audits, recalls or customer questions. It’s a smart way to secure transparency and strengthen trust across the supply chain.
4. Labeling
As you know, accurate labeling is a foundational element of good traceability, helping you meet strict regulatory standards while maintaining transparency with consumers. A specialized food ERP can auto-generate labels that pull in real-time traceability data—like country of origin, batch numbers, allergens and expiration dates—taking the pressure off your team and removing the guesswork. Since the data comes straight from your ERP system, you can count on every label being consistent, accurate and regulation-ready. That’s key when you’re shipping across regions with different packaging laws or tying to avoid costly mislabeling issues that could cause a recall, or worse, make someone sick.
But this isn’t just about staying compliant. A good packaging and labeling setup also saves your team serious time. Instead of creating templates from scratch or copying data manually, your employees can select the fields they need, apply filters and generate labels tailored to specific customers, vendors or product types. You can even route labels to different printers by location, employee role or work center—so your warehouse flows without a hitch. This setup helps you ensure transparency and compliance with evolving regulations that your consumers expect, all while keeping your production line moving smoothly.
5. Product Specifications
When it comes to managing your food product data, scattered spreadsheets and siloed systems just don't cut it. You need a traceability solution that gives you a single source of truth—capturing detailed information like ingredients, additives, nutritional values, allergens, dietary considerations, country of origin and even packaging details. A food ERP delivers just that. And the best part: Once your raw material specs are in place, those values can automatically flow into your semi-finished and finished product records using your production or assembly bill of materials (BOM). That means no more duplicate data entry or version control chaos—just accurate, up-to-date product information your team can rely on.
So, centralized product data supports stronger traceability. Accurate labels and packaging ensure consumer transparency and help you meet regulatory requirements with confidence. Allergen information and dietary details are clearly tracked, making it easier to prevent cross-contamination and manage risk. And because everything is tied to your item numbers and BOMs, your team can access the right specifications instantly—minimizing errors and making sure traceability information is correct the first time. Whether you're updating a formula, comparing supplier versions or preparing compliance documents, the details are complete, consistent and ready when you need them.
6. Compliance Document Management
Staying up to date with changing food traceability regulations is non-negotiable. But managing regulatory paperwork across your supply chain can quickly become a logistical nightmare. Between safety data sheets, producer certifications, quality test reports and vendor documentation, the volume alone is enough to overwhelm your team—never mind the complexity of each vendor-item combo having its own specific requirements. With an industry-tailored food and beverage ERP, you can digitally store and assign all necessary documents at the item, item group or vendor level—making it quick and easy to call up the relevant documents in the case of audits, inspections or recalls.
You also don’t want surprises when it comes to expiration dates. Compliance documents aren’t “set it and forget it”—they need regular review and expired certificates can lead to food safety risks and traceability violations. Regulatory audits can happen anytime, so it’s important to keep all documents organized and easy to access. The food ERP system helps you stay audit-ready by storing everything in one place. Better still, the system alerts you before a certificate expires with visual flags and automatic reminders for the responsible staff. So whether you’re placing an order or checking incoming goods, you’ll know the right documents are in place and up to date.
7. Integration With Barcode Scanners
If you’re still relying on paper-based systems to manage your warehouse, it’s time for an upgrade. Integrating barcode scanners with your food traceability software transforms the way you handle inventory—from receiving and storing to picking and shipping. With handheld devices in your employees’ hands, every scan feeds data directly into your ERP system, updating lot numbers, movement records and stock levels in real time. No more handwritten notes, no more delays in data entry and no more errors from manual input. Just faster, cleaner workflows that ensure traceability data is cleanly collected at every step in your supply chain.
What does this look like in practice? Say your inbound team scans a new delivery—it’s instantly recorded and traceable. Your outbound crew picks from the right lot because the system confirms it. And your production staff don’t have to chase down paperwork to know what’s been used. Since each barcode scan is tied to digital records, your traceability improves automatically, helping you stay audit-ready and confidently track every product’s movement. What’s more, you can assign mobile profiles by role, so each team member only sees the tasks they need—keeping things focused, accurate and efficient from end to end.
8. Supplier Certifications
Managing producer and supplier certifications can quickly spiral into chaos—especially when you're juggling direct vendors, third-party growers, warehouses and co-packers. That’s why a centralized system to track certifications and audit documents is critical to maintain end-to-end traceability. An ERP for food businesses assigns valid quality certificates to lots automatically, even when multiple ingredients or suppliers are involved. This kind of automation ensures that only compliant, up-to-date documentation is linked to your inventory, minimizing regulatory risks and making your next audit feel like a formality instead of a fire drill.
What your business needs is less scrambling for the right paperwork and more confidence in your sourcing decisions. Supplier certifications become easy to monitor and verify at every stage of your supply chain—from raw material intake to finished product delivery. If a certificate expires or goes missing, the system flags it before it turns into a compliance issue. Plus, when your customers or partners ask for proof of quality, you can produce it in seconds. That kind of transparency builds trust and keeps your brand's integrity intact.
9. Approved Suppliers
When it comes to safeguarding food safety and quality, your supplier list is where it all begins—and where things can just as easily go wrong. A robust traceability system should give you the power to lock in approved vendors and block any that don’t make the cut. This ensures that only pre-qualified sources are used in your procurement workflows, significantly lowering the chance of non-compliant, untraceable or low-quality materials entering your production lines. It’s one thing to trust your team’s judgment—it’s another to have a system that backs them up with pre-approved parameters.
With the traceability features of a specialized food ERP, you can track supplier status down to the item level, enforce tighter quality standards and maintain full control over who supplies what. Whether you're managing five suppliers or fifty, you're better equipped to reduce risk, improve audit readiness and ensure compliance with customer or regulatory expectations. In reality, a good traceability system does more than store names on a list—it empowers your team to build a supply chain of trading partners that operate with your same high standard.
Excel in Traceability and Food Safety With Aptean
Considering just how crucial traceability is for food and beverage companies—and how challenging it can be to track all the details on your products from one end of the supply chain to the other—it makes sense that purpose-built technology is the best solution. And in terms of food traceability software, industry-specific food ERP systems are considered the go-to answer.
Aptean Food & Beverage ERP shines thanks to the robust traceability functionalities covered above, as well as the option to deploy from the cloud on the Software as a Service (SaaS) model. This flexible and lightweight setup can afford your business greater scalability, enhanced data protection, stronger cybersecurity and broader accessibility.
We also have a team of experts with decades of collective experience with the food and beverage market, which helps them develop and continually support unique technologies that facilitate the highly specialized processes necessary in your industry. We truly “speak your language” and know how to implement best practices for manufacturers and distributors.
Finally, we’re proud to be leading the way in next-generation technology with advanced artificial intelligence (AI) capabilities that are already helping many of the industries we serve. Our AppCentral platform brings your industry-specific ERP together with advanced apps for asset management, business intelligence, transportation and more in one easy-to-use, connected environment. It’s designed to improve efficiency, reduce manual work and support smarter decision-making across your operations.
With Aptean, you’re not just choosing today’s software—you’re preparing for tomorrow’s smarter, more connected systems.
If you’d like to learn more about how software can help you maintain food traceability with standardized processes, check out our 4 Steps to Create Excellent Food Product Traceability Procedures and feel free to contact us with any other questions.
Start increasing traceability in your operation
If you’re ready to take your food or beverage business to the next level, we’d love to help.
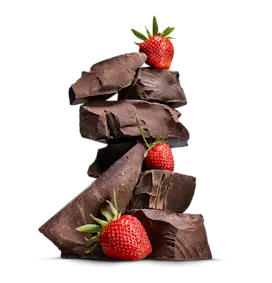