Top 4 Reasons Your Apparel Manufacturing Company Needs Shop Floor Control Software
Top 4 Reasons Your Apparel Manufacturing Company Needs Shop Floor Control Software
Top 4 Reasons Your Apparel Manufacturing Company Needs Shop Floor Control Software
May 10, 2022
Aptean Staff Writer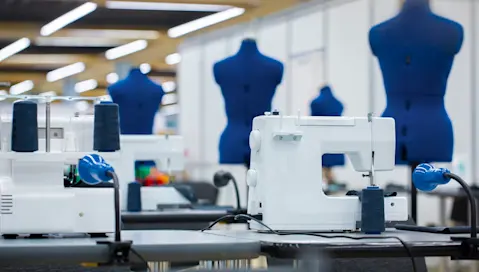
Let’s say you’re the production manager for a growing soft goods manufacturing company. If the CEO asked you, “What’s happening on the shop floor right now?” Would you know how to answer them?
Do you know where the bottlenecks in production are? Can you easily calculate incentive pay in real-time, or accurately forecast production? If you can’t answer any of these questions with confidence, you need shop floor control (SFC) software.
What Is Shop Floor Control Software?
Shop floor control software is a dedicated system that enables both production managers and C-suite executives to collect, track, access and process relevant production and payroll data from the factory’s operations–in real time. For apparel, fashion and consumer goods manufacturers, you need to improve efficiency, productivity and product quality. At the same time, you also must track sustainability metrics, fulfill compliance requirements and maintain complete visibility.
Before SFC was invented, most companies operated on the “batch” system, which is a paper-based method for collecting the data on production at the end of each day and then collecting all the data later. Then the information is entered into a spreadsheet for analysis and payroll. Obviously, this method is labor-intensive, and manual processes are always prone to human error.
Shop floor control software captures time and performance data on all production activities in real-time. With user-controlled dashboards, you can see key performance indicators (KPIs) for individuals, product lines, teams and more. In short, SFC lets you keep track of operations and processes in the facility—or in multiple facilities—simultaneously. It gives you total control over the shop floor, and lets you know when issues arise immediately.
You Need Shop Floor Control: 4 Reasons Why
Exenta from Aptean Shopfloor Control is browser-based software that is not only user-friendly for any workers, but it can be customized to meet any company’s needs. It’s Structure Query Language (SQL)-based, so it supports modern corporate infrastructure, and each user can tailor their dashboards so they always have the information they need at hand.
Each worker, or team, gets their own tablet where they keep track of each finished item for which they are responsible. A scan-and-work system guarantees accurate counts, and problems with machines or downtime get recorded immediately. With auto “always on” scanning, workers and teams can operate the system without ever having to touch the tablet. They just scan and work. The system also has full document delivery, with pictures and videos, which greatly improves delivering information to the workers and improves training processes.
It’s clear that Exenta from Aptean Shopfloor Control software can immediately improve your operations. Let’s dive into the four key benefits in a little more detail:
1. Rapid-fire ROI
As a manufacturer, maximizing production is your goal, and SFC software can help you achieve that. You’ll get invaluable, real-time insights into how the production floor operates, so that that you can ultimately achieve shop floor excellence. In addition, you can unlock greater efficiency by optimizing your machine use, inventory, staffing and other variables.
Exenta from Aptean SFC is easy to install and deploy in any environment, and it isn’t dependent on a broader tech infrastructure. In fact, in one installation in rural Colombia, most workers didn’t have smart phones, and the only internet available was DSL-based. However, the team had it running in mere hours. The software is easy to understand, so the staff immediately adapted to using it in their daily routines. The factory started seeing results in just a few weeks.
Some clients saw a return on investment (ROI) within a month, with an average ROI of 4 months. How? Simply by increasing productivity, saving on time and reducing excess labor. The biggest ROI gains come from plant efficiency. Most companies that adopt SFC have noted 77% rise in production efficiency, with some enterprises reporting even higher numbers. Moreover, many enterprises noted a reduction of more than 25% in absenteeism and approximately 75% reduction in overtime hours.
But the benefits don’t stop there. The system saves time because it avoids queues at the time clock. While it sounds minor, clocking in and out—and waiting to do so—means about 5 to 15 minutes per operator, per day. By eliminating the time clock bottleneck, companies could save approximately 3,000 minutes per day. Each employee or team can clock in and out at their designated workstation within seconds.
What’s more, operators and supervisors know about any errors in real-time so they can address them immediately. In the past, if an error occurred, an operator had to stop, note down the mistake, halt production, find a supervisor and figure out how to fix it. With Exenta from Aptean Shopfloor Control, supervisors work in a proactive environment where they can resolve problems as, or even before, they happen.
Calculate how much you could potentially save with our free ROI calculator.
2. Massive Uptick in Productivity
SFC software has a proven track record with enhanced productivity across all industries using it, moving up from 20% productivity to a whopping 55%, with the standard at about 37%. Because the software ensures traceability across the production line, your team has full accountability which improves employee engagement.
The system uses individual Android tablets for all employee interactions—with operators using the tablets to scan each item as they complete them. This not only guarantees accuracy across all lines, but it also motivates your employees to keep up with goals and meet and exceed your set production standards.
Supervisors and managers receive real-time, actionable insights into quality control, machine maintenance, performance monitoring and production line balancing. When non-standard events occur, such as machine downtime, managers will know immediately and can handle the issue. In the past, most companies didn’t know what was happening on the shop floor until days later. Once they discovered there was an issue, it was often too late to resolve it.
Exenta from Aptean Shopfloor Control boosts productivity because managers and supervisors get daily reports on individual or team productivity–letting them know which of their operators consistently performs the best. They can leverage that information into best practices for team members who might be struggling, or as incentives to raise performance overall. On the other hand, operators also have visibility of how they are performing, which empowers your teams to consistently strive to improve. Manufacturers that have adopted Exenta from Aptean Shopfloor Control software realized 37% gains in productivity and 44% in quality in the first few months.
A further boon to productivity is the ability to display construction details or instructional videos on demand, which helps improve quality. On the production floor, you can display productivity, quality and other information on monitors. This keeps your managers and your workers connected and informed, which results in increased motivation and teamwork.
3. Complete Visibility
Everyone in your organization can benefit from having SFC software. For example, the production manager’s job is to ensure that deliveries are complete and go out on time. With a robust shop floor control system, the production manager can see at 9:00 a.m. that the operators are running behind.
If they continue at the current pace, the day’s delivery is not going to go out on time. They look over the analytics, make some tweaks and the order is now ready for the truck at 4:00 p.m. In addition, factory supervisors can stay more focused on operational data, such as employee attendance and productivity. They can respond immediately to quality issues and thus avoid production bottlenecks.
With delivery times moving at a breakneck pace, this kind of flexibility is what your operation needs to stay competitive and meet retailer demands.
C-suite executives will have a macro view of the organization’s performance. When coupled with information in your ERP, they can see if the company is meeting revenue, cost and profitability goals. They can analyze the different plants and see which ones are performing well compared to the others and check to see if product costs for production are not meeting profitability estimates.
4. Decrease in Overtime and Improved Employee Morale
Exenta from Aptean Shopfloor Control software helps you identify and resolve production bottlenecks, and then the system presents options for fixing production delays. It immediately establishes a cadence of continuous improvement, because your operations are standardized according to industry best practices. You can identify weak points in the production process and solve problems on the fly.
With the tablet at their stations, operators and teams receive immediate feedback. Individual operators can better pace themselves and evaluate their efficiency as well as send alerts to their supervisor or mechanic as problems (such as machine downtime) arise. Having this kind of data at their fingertips empowers and motivates both operators and teams, because it makes them feel like they are a crucial part of the achievements and goals of the company.
Supervisors can post stats on large-screen smart TVs as a motivation tool with visibility to the whole team. This encourages better performance and productivity and may discourage absenteeism. After all, if they know they will be held accountable, they are more likely to be responsible.
Because it significantly reduces worker and administrative time and expenses, shop floor control eliminates the need for time clocks, paper tickets, gum sheets and manual processes. The software is compatible with all the major payroll solutions and implementing payroll with customizable pay types supports variable pay rates for different employees, such as hourly, salary or team incentives.
SFC: The Key to Owning the Industry
If you are in soft goods manufacturing, you know that technology is essential to stay competitive. In your industry, you have an almost impossible job. Not only must you keep up with retailer and consumer expectations, but you need to maintain impeccable quality standards and you must get your product to market quickly.
With Exenta from Aptean Shopfloor Control, soft goods manufacturers obtain full visibility of every aspect of production, which streamlines administrative processes and improves the floor manager’s capability to solve production issues before they escalate. This means you can accomplish goals and remain competitive in a fast-moving, ever-changing industry.
If you need to increase production and visibility—and who doesn’t—then it’s time to look at Exenta from Aptean’s Shopfloor Control solution. With years of experience in the apparel and soft goods industry, this SFC solution designed by and for industry experts can help you achieve shop floor excellence.
Are you ready to take control of your shop floor and manage production with confidence? Contact us today to learn more about Exenta from Aptean Shopfloor Control solution or schedule a demo today.
Ready to Start Transforming Your Shop Floor?
We’ve got the specialized MES solutions you need to conquer your industry challenges.
