Featured in this post
EAM vs. CMMS: Do You Really Need to Choose? What’s the Difference?
EAM vs. CMMS: Do You Really Need to Choose? What’s the Difference?
Aug 1, 2023
Aptean Staff Writer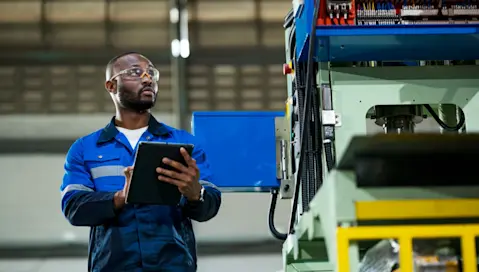
Many manufacturers have more unexpected downtime than they probably think. It’s a costly problem for most businesses, but it doesn't have to be. A recent report found that the average cost of a downtime incident is about $17,000, and manufacturers experience over 800 hours of downtime annually.
Investing in a solution to improve your organization's maintenance program is a prudent financial move along with other business benefits. When it comes to tracking maintenance and asset performance, there are two primary business solutions—computerized maintenance management systems (CMMS) and enterprise asset management (EAM) systems. Although these two maintenance-focused systems are frequently mistaken for one another, there are some distinct differences.
In this blog, we will tackle every aspect of EAM vs. CMMS and the respective benefits they can deliver to your business. Furthermore, we'll discuss how the right EAM and CMMS solution will scale as your business grows.
What Is CMMS Software?
CMMS is all about equipment maintenance. It aims to help asset-intensive industries to improve their uptime by automating scheduling, asset inventory, work order management and preventive maintenance processes. Additionally, deploying CMMS software can help you monitor your asset’s performance with scheduled maintenance work.
How Does CMMS Work?
At the core, a CMMS manages maintenance work by maintaining information like:
Work order management—this is the main objective of CMMS. It stores information like work order numbers, description, priority type, order type, personnel assignments and materials needed for repairs.
Asset details—these include the manufacturer’s name, model number, serial number, equipment class and type, asset cost, location, uptime/downtime stats, repair manuals, warranties and more.
Inventory and audit records—CMMS stores accurate records for maintenance inventory and audit.
Benefits of CMMS
CMMS has many benefits for an organization that is ready to move from manual methods to dedicated solution for managing your equipment maintenance.
Streamlined maintenance process and work orders—allows all departments to view work orders and notify them for scheduled and emergency maintenance work. This data and forms will be stored in a central location to prevent miscommunication and inaccuracies.
Effective preventive maintenance—automates the preventive measures so that managers can produce an advanced maintenance strategy. Schedule preventive checks every week or every month as part of the overall maintenance plan.
Automated inventory and audit control—keeps track of your replacement part inventories without the hassle of manually recording information and tracking suppliers.
If you're looking for more robust, precise and scalable software, you may want a more comprehensive solution—an EAM system.
A recent report found that manufacturers experience over 800 hours of downtime annually.
What Is EAM Software?
Enterprise asset management (EAM) software was conceived based on the idea that computer systems can help the manufacturing industries prevent equipment breakdowns, inventory inaccuracies, production inefficiencies and revenue loss. EAM systems offer more capabilities than a CMMS.
How Does EAM Work?
EAM brings positive results to the production lines of manufacturing companies by helping organizations change their maintenance program from a reactive to a proactive approach. This allows them to anticipate and mitigate operational disruptions.
Today’s EAM systems leverage accessibility and connectivity throughout the organization with the primary goal being to maximize asset utilization and performance while minimizing expenses. In terms of running and sustaining assets at affordable costs, EAM can help businesses avoid expensive emergency repairs by standardizing regular maintenance routines. It also records the asset's lifecycle, starting with its purchase and aids in the identification of underperforming assets.
Benefits of EAM
A well-planned maintenance program helps increase your profitability by improving the productivity of your machines while lowering costs to maintain them.
EAM systems may help you improve your operations and give you access to information you've never had before with advanced analytics and reporting, allowing you to make smarter and faster decisions to keep your production running.
Access to asset performance and maintenance data is available whenever you need from anywhere at any time if you deploy a cloud-based EAM system. Whether it's KPI reports from your home office or equipment manuals, photos or instructions on the shop floor, you can proactively respond and inform site technicians and managers of emergency repairs.
An EAM system offers many benefits for your operation, including:
Improve productivity—save costs by reducing downtime with your machines always in peak shape while ensuring process compliance to avoid costly failed audits.
Greater visibility—collect and analyze data on assets and maintenance activities like live work and order status tracking to show progress immediately across departments and site locations.
Better understanding of results—track more than 100 KPIs to help you identify patterns, trends and areas for improvement.
Simplify preventive maintenance—manage both preventive maintenance and emergency work orders. Efficiently allocate your maintenance team to prioritize critical repairs.
Minimal additional training—flexible dashboards make for a user-friendly interface. All documentation is easily accessible from within the work order.
How Do CMMS and EAM Differ?
The first difference between the two solutions is that a CMMS focuses more on asset maintenance and can only track assets upon acquisition and installation. On the other hand, EAM has more extensive capabilities that can monitor and preserve the entire lifecycle of your equipment starting from the design phase through specification requirements and installation.
Most of the time, CMMS systems manage a specific location for maintenance, while EAM systems can handle multiple site locations and even different business models if you wish.
A more straightforward comparison between these two systems is that EAM includes everything that can be found within a CMMS, but with additional capabilities. Hence, if you decide to deploy an EAM system, you'll get a CMMS included plus many other functionalities to help your operations.
The great news is that manufacturers don't have to choose between EAM vs. CMMS. There are solution providers like Aptean that offer an EAM solution that covers all the capabilities of CMMS with additional functionalities. If you're looking for the ideal EAM solution, you may explore providers that let you start with the basic features fit for a CMMS. Then, as you scale and grow, they allow you to enable additional functionalities based on your business needs.
“It was just a no-brainer to start moving forward with this new more modernized and user-friendly system, it was a natural progression to move to the modern version of what is really very good software."
Identifying the Best EAM: Aptean's Solution Stands Out
As manufacturing companies embark on their digital transformation journey, they need to consider an industry-specific EAM system and one that can scale as their business grows. How would you like to optimize asset performance, minimize asset downtime and reduce maintenance costs? Read the story below of one of our Aptean EAM customers who did just that.
UFP Industries, one of the top 100 Fortune 500 firms, has used Aptean EAM since 2013 for their asset and maintenance management. As they grew and expanded use of Aptean’s EAM solution to multiple warehouse locations, UFP Industries migrated to the cloud to efficiently manage their physical assets with ease.
“It was just a no-brainer to start moving forward with this new more modernized and user-friendly system," stated Trenton Mattingly, Maintenance Systems Integrator, UFP Industries. "It was a natural progression to move to the modern version of what is really very good software."
Being an EAM solution that grows with your business to tailor-fit your proactive asset management needs, Aptean EAM has all the features in an easy-to-use solution that will benefit all business types.
Aptean EAM stands out with these unique benefits:
Scalable to all business needs. Aptean EAM offers multiple versions designed to meet your current needs. It covers core features to advanced capabilities depending on your requirements. As your business grows, you can scale the solution and functionality to meet your needs.
Anywhere access. Aptean EAM is cloud-based, meaning you can stay updated on your maintenance needs from anywhere—your shop floor, the office, at home or on the road. We also offer a mobile app to help improve the usability and mobility of the solution. Now, technicians can manage their work orders on the shop floor instead of going back and forth between a computer and the problem asset.
Facilitated decision-making. Aptean EAM generates hundreds of KPIs and reports to help you make smart decisions. You can identify patterns that alert a more extensive issue or study it to determine if replacing the asset makes more sense than doing the same repair multiple times.
So, whether you're in the food and beverage or industrial manufacturing industry, Aptean’s mission is to help manufacturers and distributors effectively run and grow their businesses.
If you're ready to discover more about our enterprise asset management system, Aptean EAM, and its benefits like improved productivity, greater visibility and simplified preventive maintenance, don’t hesitate to reach out today. You can also request a personalized demo or a quick discovery call with an Aptean expert now.
Ready to start transforming your business?
We’ve got the specialized EAM solutions you need to conquer your industry challenges.
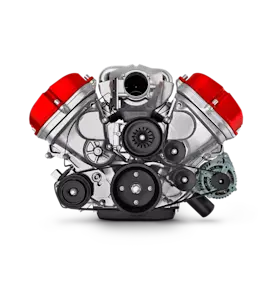