Quick links
Aptean Industrial Manufacturing ERP, Traverse Edition - Manufacturing Software
Aptean Industrial Manufacturing ERP, Traverse Edition - Manufacturing Software
Jan 14, 2019
Aptean Staff WriterHeadline
- Designed To Support Your Manufacturing System
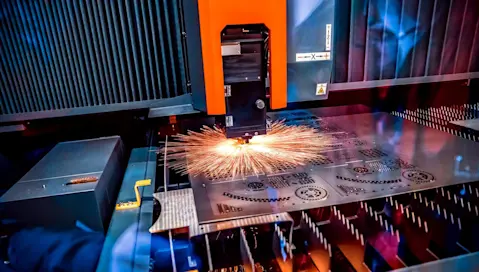
With integrated Manufacturing Software you can boost your MRP System across the board and keep your finger on the pulse of production. While you’re reducing costs or managing compliance mandates, you also need to respond quickly to both changes in the manufacturing industry and the demands of your customers. Manufacturing ERP lets you make faster, more knowledgeable decisions by giving you a complete view of your company in real time.
Manufacturing Software can help your business stay competitive with:
Forward and backward lot traceability
Reduced costs and increased margins
Managed inventory across multiple locations
Integrated scales and other hardware
Make-to-stock, assemble-to-order, make-to-order, or engineer-to-order options
Attached regulatory and compliance reports
Production Application
Aptean Industrial Manufacturing ERP Traverse Edition Production Software helps you manage all aspects of production with one application. From simplified order planning to easy access to competition status of current orders, you can manage your production processes efficiently. Easily import information from your critical data-gathering equipment such as barcode readers, time card systems, and more. Use the reporting tools to analyze sales orders, get to the bottom of variances, and more.
Production Management features:
Perform visual drilldown and production order editing
Use priority-based dispatching
Set up multiple costing methods
Conduct online status inquiries of ongoing production
Bill of Materials Application
The best way to define, track, and review your manufacturing activity is to start with Aptean Industrial Manufacturing ERP Bill of Materials. Regardless of their complexity, you'll be defining bills of material with features such as mixed unit of measure, multiple routing definition, detailed routing, cross-group costing, scrap tracking, and total visual documentation. Robust reporting gives you quick access to vital manufacturing information
Manufacturing Bill of Materials features:
Use stock or non-stock components
Perform global replacement of components
Create user-defined cost groupings
Apply optional routing definition
Requirements Planning Application
Looking to hit inventory goals more closely, with as little overage or shortage as possible? Aptean Industrial Manufacturing ERP Requirements Planning helps determine not only which items you need, but when you need to purchase them in order to achieve your company's sales goals. Whether your preference is for bucketless views of your future inventory needs, or for standard Requirements Planning reports, Aptean Industrial Manufacturing ERP will help you increase your inventory forecasts.
Requirements Planning features:
Lead time management
Component pegging
Automatic purchase requisition generation
Interface to Bill of Materials/Kitting
Routing and Resources Application
The perfect complement to the Bill of Materials module, Aptean Industrial Manufacturing ERP Routing and Resources helps define labor, machinery, tooling, and work centers. In terms of costs and times, these elements make up the process side of the manufacturing bill of materials. After helping you define elements of your operation, you can create step-by-step routings for use in the Bill of Materials application. The Routing and Resources application provides true production flexibility.
Routing and Resources features:
Calculate overhead by labor, machinery, piece, and/or flat rate
Set up required labor by machine group
Define tooling by operation
Estimate billing rates
Configurator Application
With Configurator, you can create a set of questions, choices, and guidelines to simplify the assembly process. Aptean Industrial Manufacturing ERP Configurator automatically sets up new item IDs, bills of material, and production orders as needed to expedite manufacturing.
Configurator features:
Create prompted rules and constraint-based workflow processes
Automatically set up Item IDs and bills of material
Capture quality management control information
Make to Stock
In a Make to Stock production environment, the product is manufactured to completion before receipt of a customer order. Typically the items and quantities to be made are based on a forecast of demand with the advantages of this strategy being very short lead times for shipping product and very well defined production methods and times. Strong Material Requirements Planning (MRP) and tight inventory control are mainstays of this strategy.
Make to Stock features:
Demand driven by sales forecast
Master Production Schedule to manage goals
MRP reporting in bucketless or user-definable buckets
Inventory visibility across multiple warehouses
Cycle counting, inventory tags, and import from handheld devices
Post production backflushing
Make to Order
With Make to Order manufacturing, the product is manufactured after the receipt of a customer order. The items and quantities to be made are based on customer orders. Lead times for production are typically longer than in a Make to Stock environment. Flexible production is a must in this environment. In many cases components are purchased specifically to produce products for customers.
Make to Order features:
Online printing, faxing, emailing of sales documents
Ability to partially close production orders
Drag-and-Drop dispatch scheduling for rush jobs
Wireless shipping and receiving
Extensive pricing capabilities
Purchase price variance tracking
Assemble to Order
In an Assemble to Order production environment, the product's major components are manufactured to a subassembly level and placed in stock. Upon receipt of a customer order, the specific configuration the customer ordered is run through a final assembly phase and shipped. The subassemblies are based on forecast and demand, the advantage of this strategy being short lead times for shipping a product, but with a good degree of flexibility. Strong MRP, tight inventory control, and flexible production order processing are essential to this strategy.
Assemble to Order features:
Ability to build subassemblies to forecast
Production work orders automatically generated from sales orders
Very flexible production work order maintenance
Real time inventory updates
Component pegging
Bill of Materials Kitting for single level bills
Job Shop
Within a Job Shop production environment, a company can simply perform a service for customers, such as machining services and/or produce a product. In the case of services only shops, there is typically a short turnaround time for customer orders, with a high emphasis placed on job status reporting and accurate labor and materials costing to the job. In addition to these requirements, a shop that produces a product will require tight inventory control and the ability to buy parts and materials to the job. Flexible job scheduling is also a requirement.
Job Shop features:
Production work orders automatically generated from sales orders
Ability to partially close production orders
Reporting of bills at last cost
Outside services automatically tracked and paperwork prepared
Shop calendars
Tooling definition and attachment to operations
Engineer to Order
With Engineer to Order, the company provides both engineering services and job shop services and products. There are typically long lead times for this environment, because the final product is custom designed and built. A strong emphasis is placed on job status reporting and accurate labor and materials costing to the job, including subcontract management. Tight inventory control and the ability to buy parts and materials to the job are required. In many cases the company provides aftermarket parts and service on the equipment they produce.
Engineer to Order features:
User-defined cost groups
Cost estimating through Planned Bills or Planned Production Orders
Complete shop travelers with optional bar coding
Extensive variance reporting of actual against estimate
Ease of recording activity to production orders
Ability to to generate PO directly from Production Order
Project Manufacturing
In a Project Manufacturing environment, the company provides engineering services, job shop services and on-site services to install the product that is produced. A strong emphasis is placed on job status reporting and accurate labor and materials costing to the job, including subcontract management. Tight inventory control and the ability to buy parts and materials to the job are required. In many cases the company provides aftermarket parts and service on the equipment they produce. This environment typically has the longest lead times.
Project Manufacturing features:
Buy to the job capabilities
Billing the project and phase levels
On account deposits tracking
Multiple billing formats supported
Overhead allocation and reporting
Revenue and profitability reporting by project
Want to learn more about how our industrial manufacturing ERP, Aptean Industrial Manufacturing ERP Traverse Edition, can help your business? Contact us today to chat with one of our experts or schedule a demo.
Related Content
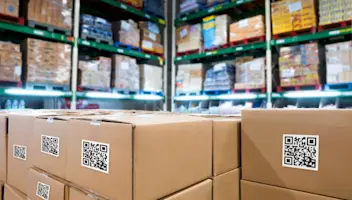
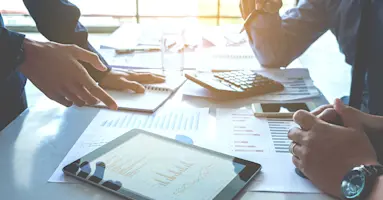
Start transforming your business today
If you’re ready to take your discrete and industrial manufacturing business to the next level, we’d love to help.
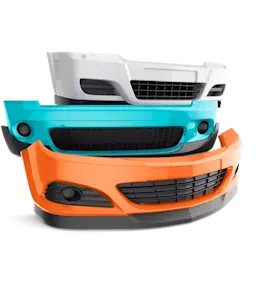