The Future of Supply Chain Management for Manufacturers
The Future of Supply Chain Management for Manufacturers
The Future of Supply Chain Management for Manufacturers
Apr 22, 2021
Daniel Erickson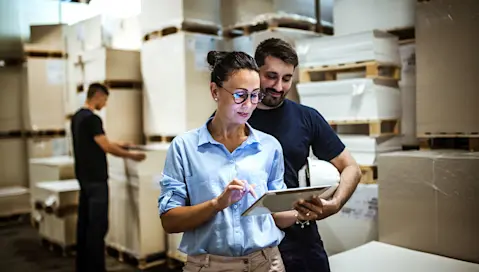
The coronavirus pandemic reminded manufacturers and the public alike of the fragile nature of the supply chain. As shortages of previously plentiful goods hit stores across the United States it quickly became clear that a greater resilience to catastrophic events would be a necessity going forward.
A year on, what does the future of supply chain management look like?
One thing that the pandemic has made clear is that manufacturers must equip themselves with the right tools and processes to mitigate future risks and weather supply chain disruptions as they arise.
Post-COVID Effects on the Supply Chain
Many businesses struggled to adapt with flexibility to the real-time shock of the COVID-19 pandemic, highlighting the need to be prepared for catastrophic or “black swan” events. These challenges could include weather events (fire, flood, tsunami), disease outbreaks, worker strikes, social unrest, trade wars, labor disputes, product demand spikes, supplier bankruptcy and many other disruptions.
In an effort to be more flexible and adaptable in the future, manufacturers may favor more local-based suppliers, rather than sourcing globally. If international suppliers are a necessity, depending on suppliers from only one country will likely be avoided if possible.
To eliminate reliance on single-source suppliers, companies will seek out more diversity to assure continuity of supplies in difficult times—spreading out risk. While manufacturers may not completely move away from a Just in Time (JIT) model of inventory, many may adjust their thinking regarding maintaining higher inventory stock levels in case on-hand materials become hard to get during a crisis.
An increased emphasis will be placed on strengthening supplier associations, as these connections can be invaluable during times of difficulty. Efforts will likely also be made to attain status as the “customer of choice” for key suppliers by cultivating relationships and maintaining consistently good levels of communication.
How ERP Can Help
Supplier and Alternate Vendor Management – To ensure you can acquire raw materials from trusted vendors, a manufacturing ERP solution stores supplier information including materials available for purchase, applicable certifications, quality control results and risk assessments. Qualified alternate vendors are also vetted and ranked, should a primary supplier’s materials become unavailable.
Vendor Scoring – The performance of primary vendors and alternate suppliers’ is monitored by the ERP system solution so that any disruptions can be quickly identified and addressed. This is done with vendor scorecards as well as the use of key performance indicators (KPIs)—measuring the quality of goods and services, price and delivery dates.
Real-time Information – An ERP solution provides an overview of the entire supply chain in real time. This up to date and accurate information enables the maintenance of a consistent inventory.
Bill of Materials (BOM) Tracking and Revision Control – This feature in an ERP software system enables manufacturers to switch out comparable raw ingredients (if possible) when original materials are unavailable—helping to avert problems during a supply chain crisis to meet customer demand.
Aptean Process Manufacturing ERP meets the needs of manufacturers who are looking to mitigate the risk associated with disruptions in the supply chain. Contact us for a personalized demonstration.
Get in Touch Today to Speak to a Software Industry Expert
To grow your business, you need a purpose-built ERP for process manufacturing. We're ready to help—reach out today for your free no-obligation consultation.
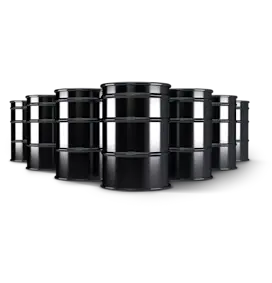