Featured in this post
Reality Check: The Manufacturing Digital Transformation Disconnect
Reality Check: The Manufacturing Digital Transformation Disconnect
Apr 1, 2022
Aptean Staff Writer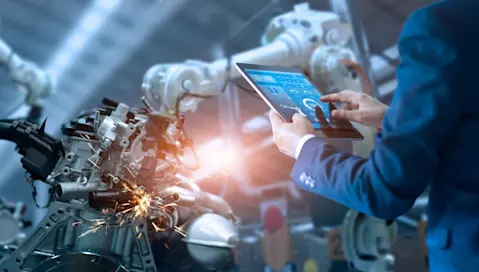
Digital transformation has been a medium or near-term manufacturing objective for several years. But market fluctuations have brought the business case for technology investment to the top of manufacturers’ priority lists.
Smart technologies and connected decision-making have become critical to maximizing operational speed and efficiency—helping manufacturers to find growth opportunities when they don’t know where the industry is heading next.
But while many manufacturing company leaders have developed a manufacturing digital transformation strategy, fewer are executing these plans quickly, creating a cognizant dissonance gap between how technologically advanced manufacturers believe they are and how their business runs day-to-day.
To understand the consequences of this manufacturing digital transformation disconnect, Aptean surveyed 275 North American manufacturers on their current automation capabilities and future plans.
In this blog, we'll cover where manufacturers fall on the digital transformation curve, how automation influences customer relationships and operational efficiency, which technologies will drive company growth in the years to come and key action points for manufacturing executives.
Question 1: Where Are Manufacturers on Their Digital Transformation Journey?
Our research discovered that 66% of manufacturers already have a digital transformation roadmap in place for some or all departments, while 72% of organizations categorize themselves as quick to adopt new technologies.
Yet, when it comes to executing this roadmap, there’s a difference in manufacturers’ perception of transformation versus their actual software investment.
For example, our survey found that 4 in 10 manufacturers have undeveloped (nascent) or non-existent digital capabilities, yet almost half (47%) believe their strategy is mature/sophisticated.

Despite this disparity, some sectors are further ahead than others. For instance, 97% of CBD manufacturers have a roadmap in place for some or all departments – over 30% higher than the industry average – and 52% are in the final stages of completing digital transformation projects.
This marked increase reflects the fact that CBD is a fast-growing, innovative area and manufacturers must work dynamically to stay competitive.
Only 9% of manufacturers admit to not having a digital transformation strategy in place. But in reality, 22% have no clear roadmap.
Question 2: How Does Company Size Impact Digital Transformation?
While overstating digital transformation may seem harmless, our research revealed a concerning disconnect between what manufacturers believe they can achieve versus their actual capabilities. Especially in smaller businesses.
Here’s an example: overall, 92% of manufacturers say their data allows them to make sound business decisions; yet 64% admit to having significant gaps in their business intelligence.
When we look more closely at the realities of manufacturing automation, small to medium-size businesses (SMBs) are more likely to lag behind the curve, as fewer resources and limited in-house technical knowledge interfere with their digital development.
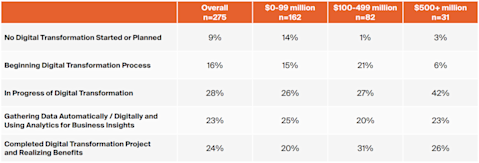
In fact, company size has a more decisive impact on automation strategies than time in business—except when it comes to experienced manufacturers.
Organizations in business for 20+ years are more likely to be relying on legacy systems and longstanding processes than investing in new technologies. And because of this, they risk being ‘caught napping’ by younger competitors more focused on innovation.
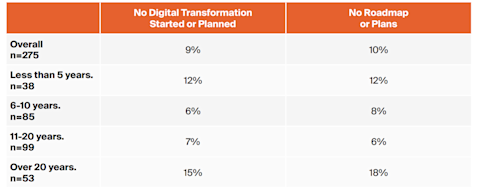
Question 3: Which Technologies Are Manufacturers Prioritizing?
Although there’s a lag between transformation goals and everyday reality, manufacturers understand the value of digital investment. And early software adoption in key business areas is demonstrating the value of automation.
34% of manufacturers say digital transformation has enabled them to increase speed of production, while 30% have improved employee productivity. In addition, 1 in 4 organizations have reduced operational costs and enhanced product quality, accuracy and consistency using manufacturing software.
We also asked manufacturers to identify which business areas they’ve already transformed through automation. Managing profit margin, calculating recipes/bill of materials and managing the production process all scored highly as tangible improvements.
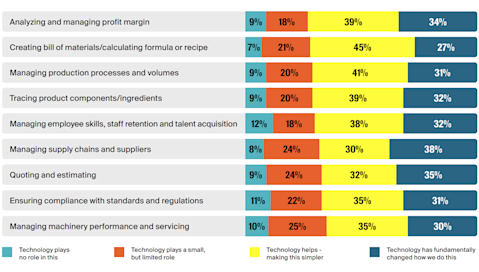
But concerningly, across the board, at least a quarter of manufacturers say technology currently plays little or no role in making their manufacturing operations simpler and more efficient; showing the untapped potential of digital transformation in almost every operational area.
Question 4: How Is Digital Transformation Impacting Financial Performance?
Digital transformation strategies are far more than a benchmark of how innovative manufacturers want to be. Technology investment is impacting how organizations are performing right now—particularly when it comes to meeting customer expectations.
As part of our research, we asked manufacturers to compare their current sales and revenue to last year and forecast their future performance. The responses we received clearly categorized companies into four different stages: struggling, recovering, recovered and prospering.
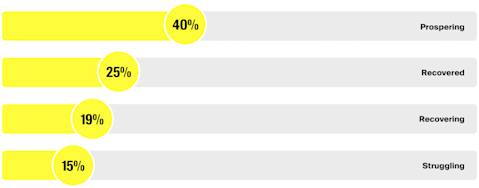
When we integrated digital transformation data into this table below, we discovered a clear correlation between how advanced manufacturers are in their technology innovation strategy and how quickly they have recovered from recent market disruption.
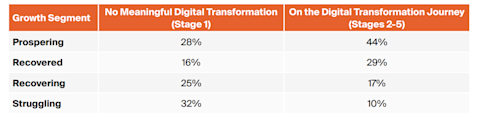
Manufacturers prioritizing digital transformation are better equipped to weather the impact of economic disruption than those who are cautious about manufacturing software investment.
Question 5: How Are Manufacturers Solving Specific Challenges Through Automation?
In addition to fueling general business prosperity, prospering manufacturers are also using automation to target performance in specific operational areas.
Almost half (43%) of the best-performing organizations we surveyed have already used technology to overcome a specific challenge, compared to just 30% of struggling manufacturers. Demonstrating that market leaders have less of a gap between their digital roadmap and actual implementations.
Below we review the percentage of companies that have already invested in a given technology to overcome a specific challenge. (Average % used across all challenges faced.)
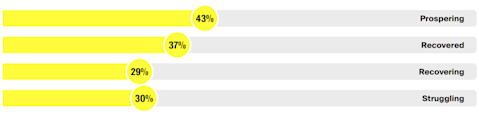
We can see this difference in action if we take a critical business area as an example: the supply chain.
Overall, 88% of manufacturers are still experiencing longer than usual lead times as a result of supply chain delays. However, 91% of the companies whose lead times have already returned to normal are early technology adopters—establishing a clear link between economic recovery and digital innovation.
Question 6: How Is Digital Transformation Influencing Customer Satisfaction?
Automation is also playing a critical role in manufacturers’ ability to meet customer expectations and then accelerate customer satisfaction.
Overall, it’s been a challenging year for manufacturing organizations, with many finding that external disruptions such as extended supplier lead times have impacted customer relationships.
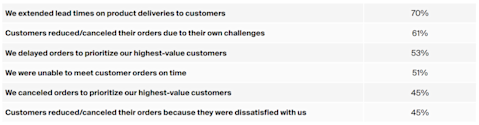
However, the increased insight and operational flexibility that digital transformation creates has enabled manufacturers in the advanced stages of their smart manufacturing strategy to manage these disruptions more effectively.
For example, 69% of manufacturers who rarely or never felt unable to meet customer demands came from the early technology adopter category—compared to just 41% of digitally cautious manufacturers.
Question 7: How Is Digital Transformation Driving Operational Efficiency?
In addition to financial performance and customer satisfaction, digital transformation is determining how well manufacturing companies manage operational efficiency. And mid-size manufacturers are in the most vulnerable position and need to act quickly.
It makes logical sense that as more processes are digitized, organizations can create orders quicker and more accurately. What’s interesting to note, however, is which operational areas manufacturers are focusing on first in their digital transformation journeys. And the biggest difference is not being driven by economic recovery stage, but by business size.
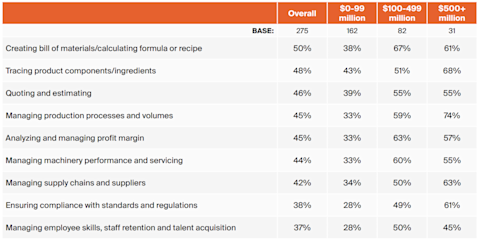
Earlier, we identified SMBs as being more likely to be in the early stages of digital transformation, and this is reflected in our data on current software investment. Compared to larger competitors, a lower percentage of smaller manufacturers have automated operations in every business area.
And while digital capabilities balance out as company size increases, there are still areas where enterprise manufacturers are likely to be ahead of the field—such as automatically tracing product ingredients, managing the supply chain and meeting compliance standards.
These are areas where mid-size manufacturers will need to invest quickly if they want to ensure their growth trajectory doesn’t compromise production transparency, efficiency and reliability. Digital innovation and process automation will empower them to remain market-reactive and quality-driven as they expand towards enterprise level.
Question 8: What Is the Golden Thread Connecting Manufacturing Digital Transformation Strategies?
While investment priorities depend on individual business challenges and goals, there is a golden thread that runs through every area of digital transformation. And that golden thread is: real-time data.
As companies integrate more processes and start connecting production end-to-end, manufacturing technologies are generating an increasingly sophisticated pool of business data. Using this data to share clear, cohesive insights will ensure that every manufacturing decision is based on the latest internal and external information—and is therefore contributing to business growth.
With 77% of manufacturers still manually collecting and analyzing data, there is a huge opportunity for manufacturing software to make intelligence gathering and interpretation more efficient.
Within companies in the advanced stages of digital transformation, this deep level of data intelligence is paving the way for machine learning, so they can begin to model potential outcomes to every market scenario, developing automated best practice responses.
However, to reach predictive modeling, most manufacturers still need to work on the visibility and accuracy of their operational data.
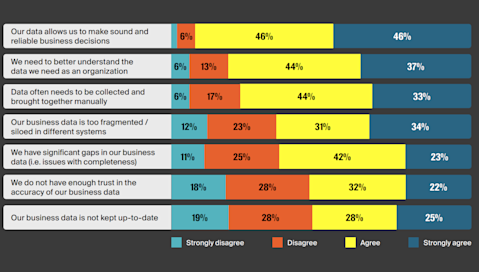
Question 9: How Does Company Size Affect Data Capabilities?
While access to real-time data is a critical objective for all companies, mid-size manufacturers are most in need of rapid operational insight.
Our research revealed that manufacturing organizations with a turnover of $100-499 million are more likely to have siloed business data, and struggle with data completeness.
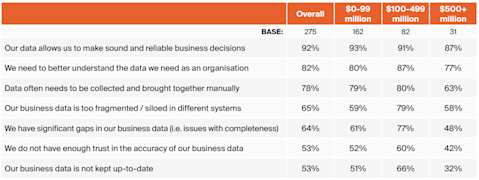
This is because many mid-size manufacturers have undergone a period of significant growth, and their infrastructure is not keeping pace with customer demand.
Legacy systems and processes can power manufacturers through the nascent stages of digital transformation. However they can’t provide the level of connected action and smart decision-making needed to scale operations and meet customer expectations long-term – which is what manufacturers that have completed digital transformation projects can achieve.
79% of mid-size manufacturers say their business data is too siloed—compared to 59% of SMBs and 58% of enterprise manufacturers.
Question 10: How Will Digital Transformation Underpin Business Growth?
Through our analysis, we’ve benchmarked how technology investment is shaping manufacturers’ current performance. But how will it influence future growth strategies?
When we asked companies about their top priorities for the next 12 months, respondents at every stage of their manufacturing digital transformation shared common goals.
The top objective now is to improve customer satisfaction (shared by 39% of respondents), followed by acquiring more new customers (35%) and improving operational efficiency and integration (33%).
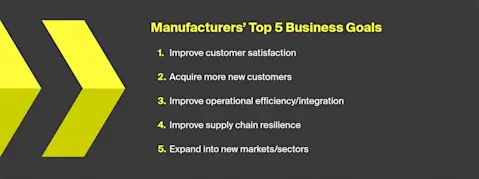
However, when we segmented manufacturer goals by digital transformation stage, those at the beginning of their automation journey have a very different set of priorities to companies that have already digitized their operations.
Technologically advanced manufacturers are focused on utilizing their data insights and digital processes to shape their business culture and move from a reactive to a predictive planning model.
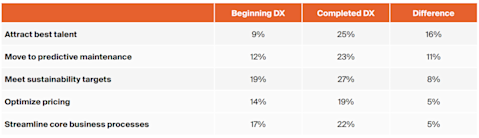
The ambitious goals should open the eyes of manufacturers in the early stages of digital transformation. Mature competitors have moved beyond automation for efficiency; they are now exploring its deeper capabilities—and this is going to influence which technologies they buy next.
Question 11: How Quickly Will Manufacturing Embrace Robotics?
Up to this point, we’ve looked at how manufacturing software can drive operational efficiency and effective decision-making. But innovative organizations are looking beyond optimization technologies to nextgen solutions that change the entire structure of their business.
One powerful example of innovation in action is manufacturers’ attitude towards robotics. When we asked companies about their attitude towards the rising role and use of robots, 88% were open to the idea, showing a strong interest in using them to take over dangerous, high risk and low value tasks.
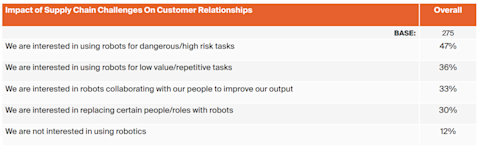
When we isolate the data for respondents who have completed manufacturing digital transformation projects already, appetite for robotics is even higher: 95% are interested, with 55% wanting to use them for dangerous tasks and 45% for low value repetitive tasks.
Interestingly, digitally advanced manufacturers are more likely to replace people with robots (36% versus the industry average of 30%), so we may see the shape, size and skillset of the manufacturing workforce evolve as automation increases.
But remember, this group is also keen to attract the best talent through technology. So they are looking to enhance human ingenuity and focus people’s skills by implementing robotics, rather than trying to replace people altogether. It’s a major cultural reformation.
Manufacturing Digital Transformation: Now And Next
The findings we’ve shared provide a useful snapshot into the current capabilities and future role of automation in manufacturing. But what does digital transformation look like today for most manufacturers – and what should they be striving for next?
Each of the five stages of digital maturity we identified increase technology’s impact on the manufacturing business. To the point where manufacturers are using software to easily collaborate, share insights and use common processes to make connected decisions and actions.
The golden thread of centralized data insight runs through every stage. However, the extent to which manufacturing companies are able to streamline operations, innovate approaches and predict where markets and customers are heading next depends on their stage in the digital transformation journey.
Take a look at our stage-by-stage overview to identify where your business lies on the digital innovation curve and plan your next step towards smart manufacturing.
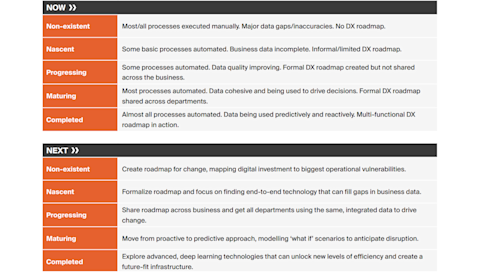
Recommended Digital Transformation Actions for Manufacturing Executives
Prioritize creating/updating your digital transformation strategy, mapping objectives to your key business challenges and goals. The stage-by-stage guide above will help you develop a logical, robust outline.
Turn your strategy into a roadmap with clear execution plans and deadlines to ensure your digital perception matches your smart manufacturing reality.
Identify technology solutions that target improvements in your key transformation areas to ensure manufacturing software delivers rapid return on investment. Focus on holistic technologies like manufacturing ERP to make sure process automation and optimization are not managed in siloes.
Improve and integrate data at every stage of digital transformation to extract the valuable insights needed to improve your operational performance and meet customer expectations.
Regularly revisit your digital transformation strategy to identify opportunities for refinement and improvement; digitally advanced manufacturers can move beyond core efficiency and visibility objectives to explore the deep value of predictive modeling and machine learning.
Kickstart Your Digital Transformation With Aptean
When embarking on such a far-reaching and transformative initiative as digital transformation, you need a partner by your side that you can rely on to deliver innovative solutions coupled with industry-specific best practice advice. That's the Aptean advantage.
As the first step and foundational core of your strategy, Aptean ERP for manufacturing drives digital transformation through a holistic approach to technology investment.
Our solution will automate your end-to-end operation, from shop floor to delivery and your organization will benefit from the following:
Increase visibility and collaboration with reliable, digital processes
Replace paperwork and automate tasks to boost productivity and cut costs
Create more accurate and dependable plans
Gain visibility into job costs and profits
Improve on-time delivery rates
Achieve maximum throughput
Make smarter operational and strategic decisions
Request a personalized demo today to discover how our manufacturing ERP and our other manufacturing software solutions can help you achieve your manufacturing digital transformation goals.
Start transforming your operation today
If you’re ready to take your industrial manufacturing business to the next level, we’d love to help.
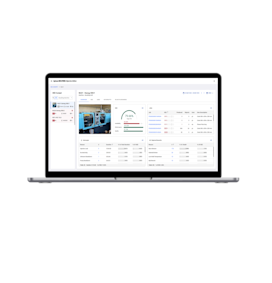