CoreFX Implements Aptean EAM for Transparency, Safety and Efficiency
CoreFX Implements Aptean EAM for Transparency, Safety and Efficiency
CoreFX Implements Aptean EAM for Transparency, Safety and Efficiency
19 Feb 2025
Ingredients producer CoreFX has come a long way since its founding in 2017. The company’s lines of spray-dried fat- and oil-based ingredient solutions, including HealthiCoreFX, NutriCoreFX and SportsCoreFX, have been embraced by the larger food and beverage industry for their many flexible applications, excellent taste and alignment with the central mission of “Health through Nutrition.”
At the center of CoreFX’s operation is Aptean’s process manufacturing-specifc enterprise resource planning (ERP) software that was implemented in early 2021. But up until recently, the company was still using manual, inefficient processes for asset management.
“I was printing all the preventive maintenance orders that we did, putting them in a binder and assigning them to the techs.”
The Challenge
CoreFX staff were still using paper records in managing the company’s equipment assets. Like any paper-based, manual processes this made administration time-consuming, inefficient and less agile. The organization’s two biggest challenges were:
Paper-based record-keeping methods growing cumbersome
A lack of high-level visibility for preventive maintenance orders
CoreFX Director of Operations, Frank Furgal, added with a laugh, “Clayton would leave every night and come to work every day with a briefcase and a folio folder. He had every single paper that he had touched for the last six months in there and he would take that thing home every night just in case he got a call.”
“We weren’t with the times. Auditors understood what we were doing, but they pushed us to get a computerized program.”
The Solution
This cumbersome method of administration, as well as feedback received from auditors, pushed the CoreFX leadership team to consider a fully digital enterprise asset management (EAM) solution. Because their existing Aptean system was deployed smoothly and performing well, the team decided to consider Aptean EAM.
“Knowing how well we worked with Aptean on the Aptean Process Manufacturing ERP rollout, we felt very comfortable working with Aptean on their integrated EAM,” Furgal said.
And so, not long after going live with Aptean Process Manufacturing ERP, CoreFX became an early adopter of Aptean EAM and began the process of working with Aptean’s experienced teams to begin the implementation.
The Implementation
At Aptean, we’re proud to work as partners alongside our clients. The regular communication during deployment and joint effort between our teams and those at CoreFX created a positive environment that encouraged collaboration throughout implementation and resulted in a smooth rollout of our EAM solution.
“One part of the implementation that I always enjoyed was having weekly meetings,” said Furgal. “It was always great to get caught up on where we were at, status-wise. They were relatively quick meetings, mostly high-level, but it was always great getting a little conversation about the different things we wanted to see. It felt like we were always making some good progress.”
The step of training all employees on the new interface was also straightforward and effective. While the change to procedures was significant, the guidance provided by Aptean and approachability of our platform, combined with the willing learners at CoreFX, led to success.
“It’s been a pretty easy transition for the entire organization. I took a role in getting everybody trained and getting them logged in, and it was all very simple.”
The Results
With much of their important asset management information relegated to paper documents with hastily handwritten notes, both Furgal and Goeke were struggling with issues of transparency and visibility of preventive maintenance and work orders prior to implementation. The difference of a digital interface and database has made a positive impact in that regard.
“It’s key to have everything at your fingertips,” Furgal said. “It speeds things up from the administration side. In an audit, you want to be able to answer the auditor’s questions as quickly as possible and move through those things to cover as much ground as you can.”
CoreFX has realized many benefits using Aptean EAM, including:
Fully digital platform maximizes visibility of work orders
User-friendly interface facilitates smooth transition to the new system
Streamlined workflows reduces administrative burden and delays
“Assigning projects to the staff is a lot easier,” Goeke added. “It’s simple for me to get the technicians the jobs that they need to do, and it’s a lot easier for supervisors and quality techs to get an issue in front of me. It takes away the delay—the techs just need to plug the information in, and it’s out there right away. They don’t have to go back to their desk to do any review—they can just type in any issue that they see.”
Another positive effect of the user-friendly Aptean EAM interface has been to improve safety and scheduling efforts at CoreFX. Both of these areas are critical for operations, as a risk-free working environment and informed planning are keys to keeping uptime at a maximum.
Now, CoreFX is looking forward to implementing the inventory management module of Aptean EAM, which should help not only with making sure replacement parts are on-hand when they’re needed, but also make tracking the financials of asset maintenance more manageable.
“We really want to have all our parts in there, like a virtual warehouse, because we’ll be able to manage our finances much better that way,” Furgal said. “We’ll be able to issue costs correctly to each asset that we have on the list, and it will also help with cash flow overall because we’ll only have to charge out when we use those parts,” he added.
“As we get this more baked into our overall culture, I would expect to see our downtime go down considerably next year.”
Aptean EAM: The Missing Ingredient for Your Operational Excellence
Whether your key objective is to reduce downtime, improve efficiency, remove administrative headaches or all of the above, Aptean EAM delivers. Our advanced solutions streamlines your and modernizes maintenance strategies with ease—helping you improve asset productivity, reduce maintenance costs and maximize profitability.
Plus, with a modular approach that encompasses both CMMS and EAM and provides access to advanced features like automated spare parts inventory control, you can be confident that our platform is ready to help, no matter where you are in your digital transformation journey, and will continue to scale with your operation as you grow.
What’s more, as CoreFX attested above, the Aptean advantage extends beyond our software to our incredible teams. Our dedicated industry professionals are on hand to ensure clear communication and smooth implementation processes, as well as offer best practice advice and by-your-side support throughout your journey with us.
To see Aptean EAM in action for yourself, take our free, self-led product tour or get in touch with our team to request a personalized demonstration.
¿Todo listo para transformar tu negocio?
Tenemos el software EAM especializado que necesita para conquistar los retos de su industria.
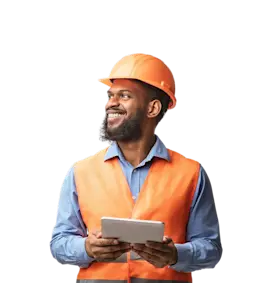