In diesem Beitrag vorgestellt
Addressing the Six Big Losses With OEE Software
Addressing the Six Big Losses With OEE Software
13 Apr 2023
Aptean Staff Writer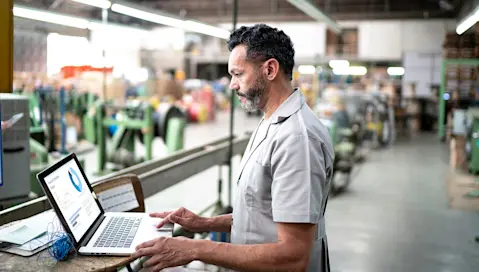
Your manufacturing business may not be perfect, but it’s your job to get it as close to that as it can be. As such, you might be considering a continuous improvement (CI) initiative—but have you considered how you’ll structure your efforts and measure your results?
From Lean Manufacturing to Six Sigma, various programs aimed at organizational improvement have come and gone over the years. These methods sometimes don’t achieve the expected results in the manufacturing world, though, because they don’t account for all of the nuances of your industry.
In this blog, we examine the importance of detailed data, smart application of overall equipment effectiveness (OEE) technology and a CI approach that focuses on the Six Big Losses. All told, your initiative will be complex and, at times, difficult, but the results will be well worth the effort.
Buckle up. Read on.
Operational Pain Points
Businesses like yours are looking for ways to optimize utilization and increase production capacity, which requires tools and strategies that are specific to your processes. You also need metrics and data, but more importantly, you need the right metrics and data, in real time, to get to the bottom of the issues arising in your operations.
You also must have accountability and buy-in not just at the boardroom meeting table, but at the factory floor level—from the shop floor to the top floor. It’s a lot to ask, but that should be expected of an effort as broad and dramatic as a CI initiative.
What will be your particular areas of concern as you map out your plan?
Data Without Details
Simply put, many standard business metrics fail to capture enough information to yield the actionable insights you need. A number that reflects poor performance will not necessarily tell you why performance was poor, after all.
With numerous machines and materials involved in your processes—not to mention plenty of quality and integrity considerations—you need to be able to drill down to specific numbers in tightly defined time ranges to really root out your business’s problems.
Manual Record Keeping
If operators and supervisors in your facilities are still using pen and paper or Excel spreadsheets to collect information, you’re lacking the visibility you need to make improvements. The delay between when an event occurs on the shop floor and the time it's recorded means the effects of whatever went wrong will already be felt, but the whole point of undertaking this initiative is to stop these errors before they happen.
Manual reporting also leaves room for human error, and the possibility of inaccuracy is enough to render all of your charts and graphs useless. Your employees need to be free to concentrate on their core tasks, not lost in the rows and columns of a table that will be questioned and likely never lead to any useful analysis.
Lack of Feedback
Perhaps your business has recognized that manual record keeping won’t cut it and deployed an OEE system to handle data capture on your manufacturing shop floor. This is a step in the right direction, but if the platform isn’t relaying up-to-date performance metrics to your staff, it’s not going to enable the kind of action that leads to improvement.
All of the numbers in the world don’t mean anything if they’re outdated.
“Relying on streams of raw data and outdated analysis can be compared to driving a car blindfolded and then getting a report at the end of the day detailing every accident you caused,” says David Gallagher, Operations Director for Greencore Cakes and Desserts, one of Europe’s leading cake and dessert manufacturers.
“A report on yield and cycle time three days later is not very useful to a busy operator whose primary task is to keep the line moving at that very moment,” Gallagher continues. “What operators need is real-time and relevant information they can use to avoid ‘accidents’ as they approach obstacles.”
Attempting a CI initiative with any of these considerations left unaddressed is a recipe for frustration. So how can you set your business up for success in this endeavor?
What Are the Six Big Losses?
The framework of the Six Big Losses in manufacturing was first laid out in the 1970s by researchers at the Japan Institute of Plant Maintenance (JIPM), and to this day this new approach to old problems stands as a solid foundation for launching a CI program.
The Six Big Losses are:
Mechanical Downtime, Loss Category: Utilization (Availability)
Set-up and Changeovers, Loss Category: Utilization (Availability)
Idling and Minor Stoppages, Loss Category: Rate Loss (Performance)
Reduced Speed Operation, Loss Category: Rate Loss (Performance)
Scrap and Rework, Loss Category: Yield (Quality)
Startup Losses, Loss Category: Yield (Quality)
To put them each in different terms, you can think of “availability” concerns as downtime, “performance” failures as speed losses, and poor “yield” results as defect losses. By breaking common problems down into these categories, your business can dig into just what’s going wrong and how to address it.
OEE Methodology
In combination with the Six Big Losses, you’ll also want to use OEE calculations to further understand how your machinery and associated processes are performing.
The equation is defined as:
OEE = Availability Rate x Performance Rate x Quality Rate
Taken as a whole, this approach can lead to improved efficiency and capacity, lower costs and better profitability. Keep in mind, though, that it’s not enough to simply be aware of these concepts—you need the sort of granular data discussed earlier to take full advantage of the methodology.
To gain that visibility you must implement the right technology - such as an OEE system - that can capture and report data in real time and maintain a steady stream of feedback for your workers. That gives them the insights they need to make informed decisions and act on the spot—preventing errors before they occur and quickly halting any runs that are faulty.
Putting the Six Big Losses and OEE Software To Use
With a relatively simple analysis, you may be able to identify that you have an opportunity to optimize your efficiency by a certain percentage. Until you break that percentage down by what proportions are attributable to each of the Six Big Losses, though, you won’t know what areas to address for positive results.
On the other hand, if you know that setups and changeovers are your biggest hurdle, you can closely examine what’s causing these procedures to lag and find solutions to the setbacks your staff are facing. Before you jump in, though, there are special considerations for each of the losses that you need to know.
Big Loss No. 1: Mechanical Downtime
It’s no surprise that downtime from equipment failure is something that manufacturers would always prefer to avoid. To actually rectify the issue, though, it takes the sort of granularity of information that we discussed previously.
Is it general wear and tear that’s causing your loss, or is it operator error? This can be captured in part with reason codes, but you really need a technological solution that can report on the root cause accurately and automatically, as that removes any room for human error or failures of memory.
You also need to empower your operators and technicians to act quickly upon any downtime information they receive—they’re the most qualified individuals to do so, after all—and monitor their performance to assess if further training is needed.
“Having an easy way to accurately track maintenance response times has helped reduce downtime by making everyone more accountable for downtime and for getting the lines back up to speed,” said one Aptean customer.
“Now when a line goes down, the operator immediately triggers an alarm for the maintenance shop,” the same customer continued. “When the technician gets there, the operator clicks the ‘maintenance arrived’ button, and the system automatically records the response time.
“In the past, it used to take maintenance up to an hour to respond. But with the increased visibility, technicians are now averaging five to ten minutes—and there’s no longer a dispute between operators and technicians about how long it took them to get there.”
Big Loss No. 2: Setups and Changeovers
An operator with no changeover target and no real-time visibility into how he or she is performing against that target cannot be expected to work toward minimizing changeover time. But in an environment in which equipment operators, supervisors and plant managers have full transparency into actual changeover times against targets, the dynamic is very different.
When provided with an allowance detailing how long each changeover should take, a video clip or diagram that explains how to complete the changeover, and an end-of-shift report that provides detailed feedback on actual changeover performance against the target, operators tend to change their behavior.
Greater clarity into root causes can also lead to significant performance improvements. The ability to analyze changeovers by crew, shift or product and to easily determine when and where performance spikes are occurring allows managers to identify potential training issues.
OEE Software in Action: Marsan Foods
Analysis into setup time variability can also reveal causes that were previously unknown or simply ignored. For instance, Marsan Foods, a manufacturer of prepared and packaged food for large retail, food service and healthcare customers, recognized that it was having problems with its “sealer”—the machine that seals food trays after filling.
Not only was it a recurring problem (it was responsible for nine percent of all downtime), but the problems only occurred at the start of the morning shift.
Improved data collection and drill-down analysis, combined with feedback from factory floor personnel, revealed that the root cause of the film breakage was excess moisture left after the machine was cleaned and sanitized overnight. By installing a more powerful air gun to dry the equipment, Marsan was able to quickly resolve the problem. Overall, the company has improved its changeover times from an average of 45 to 60 minutes, to only 34 minutes.
Big Loss No. 3: Idling and Minor Stops
Here is another area of loss for which the importance of precise, detailed data can’t be stressed enough. Readings need to be taken constantly, and feedback needs to be facilitated by an intelligent OEE system so that operators can report their findings and act on alerts with alacrity.
Frequently, the solutions to problems of idling and minor stoppages are simple and easy to implement, costing your business little to nothing in order to achieve positive results. Just remember the importance of digital solutions for minute-by-minute information capture so that inaccuracies and inconsistencies are avoided, as well as an intuitive interface for personnel to report the reason for the pause in production.
A situation that illustrates this point perfectly arose at the facilities of an Aptean client that operates in the beverage sector.
“If there were two minutes and 22 seconds of downtime, it might be recorded by one operator as two minutes and by another as two and a half,” says the client. “At daily production meetings, we would realize that we were about 70 minutes, or 5%, short on allocated downtime, according to what operators were recording in their paperwork. We knew it had gone somewhere, but it was unallocated. Automating the collection and analysis of data from the shop floor has eliminated this problem and enabled us to focus on addressing the causes of these stoppages.”
Big Loss No. 4: Reduced Speed Operation
While increasing the rate at which your lines run can certainly be seen as a positive, your aim in this aspect of operations should be to balance speed of production with product quality. If your data is reliable and up-to-date, you’ll be able to evaluate the differences in performance between different runs, operators and goods.
Gains in speed and efficiency can often be achieved simply through the additional visibility that good OEE software provides. In part, that can be chalked up to the “Hawthorne effect”—a phenomenon of human behavior that results in increased effort from individuals who are being actively observed.
It’s also due to the detailed analysis such systems can provide. Going back to the case of Marsan Foods, they were able to determine that incorrect settings after equipment changes were resulting in one line running slower than it should have. The fix was quick, and the line’s rate immediately jumped from 79% to 85%.
Big Loss No. 5: Scrap and Rework
Fixating on the size of your losses due to scrap and rework isn’t productive—what is, though, is finding out just why scrap or rework was necessary. Are products being rejected at the filler, at the capper, or somewhere else?
This is information that, as is the case in nearly every instance on the factory floor, should be collected and logged automatically, without relying on human memory or pen-and-paper methods. The combined power of Six Big Loss analysis and OEE software can also provide you with a more complete picture of the conditions at the time that production went awry, allowing you to evaluate whether other circumstances like temperature and humidity affected the resulting goods.
One Aptean food processor was able to successfully put a performance management system to use in shoring up an issue with its mayonnaise lines. Before implementing the new platform, differences in viscosity of the product had resulted in operators resorting to higher fill settings to avoid underfilling.
That, however, resulted in even more scrap—until the system was installed, timers and alerts were employed to prompt more regular examination of conditions, and automatic recording provided the immediate feedback necessary to address the problem.
“We immediately reduced giveaway by 1%, which saved us a substantial amount of money right away,” says the client.
Big Loss No. 6: Startup Losses
Losses from startup routines are frequently seen as unavoidable, but cycling a line two or three times before getting it up to full speed is simply not good enough when you’re losing product in the process. Using the best practice data collection techniques we’ve discussed here will give operators the necessary visibility to understand what causes adverse startup conditions and empower them to then address those issues.
Sometimes, revisiting your standard operating procedures can yield positive results in this area. Your employees should know the optimal setup for the processes that they work on most frequently, and recording their compliance with those requirements will encourage consistently excellent performance.
Implementing regular alerts that remind operators of the ideal rates and temperatures for your lines is another prudent measure to take, especially after a changeover to remind staff of targets right at the beginning of their shift.
Critical Success Factors in CI
Organizations begin continuous improvement initiatives with a goal of making fundamental changes. If you’re putting in the effort to launch such a program, you want to make sure you get the results you expect.
Here are the most important elements of a successful CI push:
One Version of the Truth
The best way to ensure that everyone in your organization is on the same page and that data is accurate and up-to-date is to implement a process manufacturing OEE solution for your information capture. Having one version of the truth eliminates debate and ensures that everyone is focused on addressing root causes to improve production performance.
Accountability at the Shop Floor Level
Every employee needs to feel responsible for their part of your CI program, and they need to know that when they take the right action, they contribute to the betterment of the business. Empower your staff with feedback systems that let them know their concerns are heard and inform them of the necessary steps to take to realize the improvement you’re counting on.
Closed-Loop Approach
Speaking of feedback systems, these should also provide real-time metrics by which your workers can evaluate their own performance. Rather than seeing these assessments as potential cause for punishment, factory staff tend to see them as a source of reassurance, as well as incentive to act swiftly and intelligently.
“The system isn’t used as a stick to beat the operators, but as something that gives them real measures against which they can improve,” says an Aptean beverage producer customer. “It’s a toll to help the company grow and to allow us to recognize and acknowledge improvement. It can be very motivational in that sense.”
Standard Framework for CI Deployment
This will be an organization-wide effort, so you need to ensure that important actionable information gets relayed across all of your plants and lines. You’ll only be able to achieve the results you’re looking for if your CI initiative is top-of-mind for everyone in the company—especially those on the shop floor.
Real-Time, Actionable Information
While having lots of data can be good, you should really prioritize quality over quantity here. The right OEE software can provide you with visualizations and analyses that let you determine just what’s causing your pain points, which enables you to fix what’s broken with your processes.
And don’t forget the importance of the facts and figures being up-to-date—acting on outdated information can be more harmful than not acting at all.
Easy for Operators to Use
The technological solution that you select to fuel your CI initiative absolutely must be simply and intuitive for your employees. All of the money in the world can be spent on a new system, but if your people don’t use it, that all goes for naught.
Keep in mind the importance of the terminals and displays that your factory workers will be interacting with; if they have to puzzle out the purpose of certain functions and screens, they may choose to simply ignore them, which can have devastating consequences.
Prepare for What’s Next With Aptean OEE Software
A continuous improvement approach based on the Six Big Losses can revolutionize your process manufacturing business, making it much more resilient in the face of change and far more agile in a demanding, fast-paced marketplace. But as we’ve covered here, the right technology has to be in place to really see the benefits you want.
Aptean Process Manufacturing OEE is a purpose-built solution that satisfies the accuracy and real-time requirements that the top companies need to compete. As a single, integrated platform, the benefits of implementing our OEE system will be felt across your organization and unlock the potential in your product lines.
Want to hear more about our best-in-class offerings? Contact us today to learn what Aptean Process Manufacturing OEE can do for your manufacturing business.
Leveraging Insights for Data-Driven Manufacturing Improvements
Real-time financial and efficiency metrics that OEE solutions provide can help your company act upon important insights and improve performance.
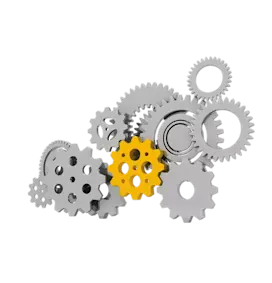