5 Steps to Create Excellent Food Product Traceability Procedures
5 Steps to Create Excellent Food Product Traceability Procedures
5 Steps to Create Excellent Food Product Traceability Procedures
3 Juni 2025
Jack PayneShort on Time? Here’s an At-A-Glance Summary
In this blog you'll discover the five essential steps for modernizing traceability processes in the food and beverage industry:
Implement a digital platform - Transition from paper-based methods to a digital solution to accurately manage key traceability details like lot numbers, expiration dates and origins.
Educate staff - Create a company culture that prioritizes traceability including training and recall simulations.
Collaborate with partners - Establish strong relationships and communication channels with suppliers and distributors to secure traceability throughout the supply chain.
Develop recall procedures - Build a dedicated recall team and clear protocols to allow for swift action, minimizing potential harm and maintaining consumer confidence.
Automate data collection - Integrate key systems such as ERP, WMS and barcode scanners to quickly and easily collect traceability data points.

From cherished childhood recipes to weekend comfort meals, food is more than sustenance—it’s a connection to who we are and where we come from. That’s why every bite should come with confidence that what we eat is safe, responsibly sourced and handled with care through every step—seed to store shelf, farm to fork. But in today’s food and beverage industry, that confidence depends on one critical capability: total food traceability.
Without it, a single unknown can escalate into a costly recall, reputational damage or worse—a public health crisis. And consumers know it. In fact, 73% of shoppers say traceability influences their purchase decisions, and 71% of those who find it very important are willing to pay a premium for it. Thus, transparency isn’t a trend—it’s an expectation.
Excellent food product traceability does more than build trust. It boosts brand loyalty, ensures faster responses when issues arise and opens doors to new markets. Yet many food manufacturers still rely on outdated, fragmented systems that can’t keep pace with modern production or supply chains.
With food traceability regulations raising the bar on recordkeeping and responsiveness, now is the time to upgrade to a robust, digital, end-to-end traceability process. After all, safeguarding your business starts with safeguarding the people you serve.
So, how do you modernize your traceability strategy to meet these rising expectations? In this blog, we’ll walk you through five essential steps to optimize your food product traceability procedure—from choosing the right software to enabling cross-functional alignment.
1. Lay the Foundation With a Digital Platform
The first step in establishing your traceability procedures for food safety will be to find the right system to use. Paper-based means don’t cut it in today’s day and age, so you’ll need to look for a fully digital solution—and it’s critical that whichever you select is tailored to food and beverage businesses like yours.
The gold standard on this front is a food enterprise resource planning (ERP) system. These comprehensive platforms serve a number of different key functions, not the least of which is to effectively implement a robust traceability plan.
Here are the key advantages of using an industry-specific food and beverage ERP for traceability:
Ability to define any number of fields for different kinds of raw material and finished product information, including lot numbers, country of origin, variety, quantity, expiration date and more
Integrations with smart devices, including barcode scanners and IoT-enabled equipment
Real-time updates based on the latest data
Ease of access, with an intuitive user interface and—in the case of cloud deployments—mobile access
While this initial measure may require investments of time, effort and funds from the exploratory research stages through the go-live date for your system, it’s crucial that you have the right technology in place if you really want to excel in traceability.
2. Educate and Train Your Staff
Even the best traceability systems can fail if the people using them aren’t properly trained. That’s why staff education isn’t just a checkbox—it’s a critical investment in your business’s resilience and reputation. Start by helping your team understand the bigger picture.
This includes explaining why traceability matters and how their daily actions impact everything from recall response times to regulatory compliance and customer trust. This broader understanding is especially critical in light of the FDA’s Food Traceability Final Rule under Section 204 of the Food Safety Modernization Act (FSMA), which enforces stricter recordkeeping and traceability requirements. With regulations tightening, your team’s ability to respond quickly and accurately isn’t just a best practice—it’s a legal necessity.
To ensure consistent processes and to minimize risk, your training program should cover:
Training on applicable regulations—such as the Food Traceability Final Rule, FSMA, Food Standards Agency (FSA) and EU traceability laws
Guidance on allergen control, sanitation protocols and preventing cross-contamination
Regular refreshers when legislation or internal procedures change
Hands-on recall simulations to keep teams responsive and confident
Clear documentation of roles and responsibilities across departments
Above all, foster a culture of accountability and shared responsibility. Every employee—from the factory floor to the leadership team—needs to understand their role in maintaining traceability. When your people are informed, empowered and aligned, traceability becomes second nature and costly mistakes become far less likely.
Is your business ready for the FDA’s Food Traceability Final Rule? Take our quick quiz to find out where you stand—and how to get ahead.
3. Collaborate With Supply Chain Partners
As the next step in the process, you’ll need to communicate with your suppliers and clients to make sure their approaches to traceability will help all parties involved achieve full end-to-end tracking of ingredients and goods. After all, your organization won’t be able to meet your goals in this important matter without the full cooperation of your business partners.
While in the past it might have been sufficient to track your materials and finished goods just one step backward and one step forward in the supply chain, that is no longer the case—you need complete visibility, from the original supplier of your materials all the way to the retail and foodservice outlets you serve.
So that no pertinent details are left out, all critical tracking events (CTEs) are covered and information is shared in a timely manner, make sure you discuss and agree upon each of the following with your partners:
What ingredient and product data needs to be captured (consult the list of examples above and aim for a comprehensive set of variables to track)
When information will be collected (including all CTEs, upon receipt and departure, etc.)
How data will be shared between entities (ideally, a fully digital format that imports to your ERP)
How frequently the information will be relayed (immediate, real-time updates are optimal)
The conversations that you have with suppliers and clients at this stage will be vital to ensuring the integrity of your data and facilitating product recalls and withdrawals when necessary.
4. Create an Internal Recall Team and Recall Plan
Speaking of product recalls, your company will clearly be aiming to avoid these issues as much as possible by employing good traceability procedures for food safety, but we must recognize that even the best-laid plans can go awry. In the event of an emergency, you’ll need to be prepared with team members to call upon for a swift and smooth execution and a clear list of steps to follow.
For your recall team, you’ll want to include factory floor staff, an operations manager, representatives from your communications or marketing department and potentially some of the higher-level decision-makers at your business. They should immediately set the process in motion with these sequential actions:
Notify all members of the internal recall team and record the incident.
Determine the risk level and assess the severity and extent of the contamination.
Send out important communications, including the relevant authorities and affected clients.
Put an immediate hold on affected products and trace the contamination back to the source.
Establish the scope of the recall and initiate the process.
File all necessary paperwork once the affected items have been withdrawn.
The comprehensive features of food industry ERP platforms can automate some of these steps, helping to ensure that all involved are made aware of the situation and all compliance regulations are followed to protect public health and adhere to all applicable laws.
5. Automate Data Collection
Before you can consider your traceability plans complete, you should strive to automate and digitize information capture as much as possible. Here again, technology is on your side, as an ERP that can integrate with your warehouse barcode system and the smart devices in use at your facilities—including thermometers, scales and sensors—can streamline the process of collection to a considerable degree.
Data-rich labels are another important part of this equation, as you want to be able to record as much detail as possible with a single scan. You’ll also need to determine when scans and readings should be conducted and the information routed to your system to update your traceability records.
You can start by using this as a preliminary list, build out your automations and expand as necessary to fit your operations:
Automatically scan barcodes/QR codes on receipt of goods and before entering into inventory.
Automate another scan at the time of picking for use in manufacturing procedures.
Monitor temperature, consistency and other pertinent factors during processing and, if possible, evaluate results with smart imaging equipment.
Create new barcodes and assign lot numbers for finished goods.
Automatically scan again upon picking for order fulfillment and again upon loading for shipment/delivery.
These measures can also help you ensure consistent product quality, as the more information you have on your finished goods will allow you to judge if your processes need retooling for improvement.
Partnering With a Provider You Can Trust
At this point, we’ve established how to create your food product traceability procedures and how vital purpose-built technological solutions are to your efforts in tracking raw materials and finished products from one end of the supply chain to the other. You may still have questions about best practices and how a food ERP system can help you maintain total traceability in the course of daily operations.
Choosing a technology partner who understands the complexities of the food and beverage industry is critical—and that’s exactly what Aptean offers. Our award-winning food ERP software is developed on the Microsoft Dynamics 365 Business Central platform—combining industry-specific functionality with an intuitive user experience. That foundation makes your traceability systems easy to configure, inherently secure and ready to adapt as your operations evolve.
What’s more, our cloud-first approach offers seamless scalability as your operations grow and enables greater data accessibility across your sites and partners, supporting stronger, more responsive decision-making. Plus, automatic updates ensure your system stays compliant with emerging traceability regulations without disruption.
We’re not just ERP providers—we’re your long-term partner in innovation. Our AI-driven solutions help food manufacturers like you lead with confidence. With our tools, you’ll be empowered to analyze trends in ingredient quality, identify potential compliance risks and proactively address issues before they escalate—all with fewer manual touchpoints and greater efficiency. At Aptean, we deliver more than software. We deliver peace of mind.
Ready to hear more about Aptean Food & Beverage ERP and how it can help you establish and implement excellent food product traceability procedures? Contact us today, or request a specialized demo. Ready to see it in action? Take our free product tour to see our food ERP functionality for yourself.
Erfolge von Aptean ERP-Kunden
Diese 10 Kunden aus verschiedenen Lebensmittel- und Getränkesektoren haben mit unserer Lösung mehr erreicht.
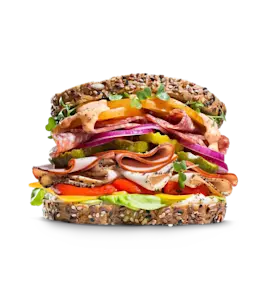