When Manufacturers Are Under Pressure, Maintenance Matters
When Manufacturers Are Under Pressure, Maintenance Matters
When Manufacturers Are Under Pressure, Maintenance Matters
May 18, 2022
Kay Jenkins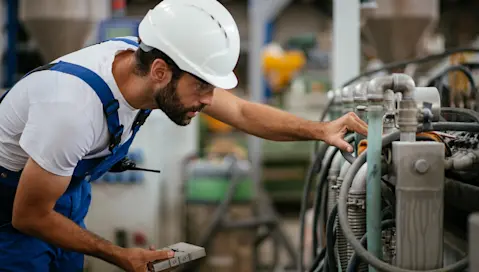
In a previous blog, we discussed what EAM (Enterprise Asset Management) software is, and what it can do for your manufacturing business. In today’s competitive climate, manufacturers need EAM software or CMMS (Computerized Maintenance Management System) to make the most out of their assets. In the fast-paced manufacturing environment, demand is unpredictable and costs are rising, so getting orders out on time, in full (OTIF) is imperative if you want to keep up with your competitors.
EAM is now a necessity. If you fail to manage and maintain enterprise assets, downtime will be the least of your worries. Malfunctioning assets lead to poor asset performance, which in turn leads to supply shortages. You need visibility into repair and maintenance trends, as well as the root causes. Plant operations excellence plays a pivotal role in maintaining and growing a profitable manufacturing enterprise.
In this blog article, we’ll examine the metrics behind plant operations excellence and how EAM and CMMS can help you achieve that, even under today’s demanding pressures to get products out rapidly. In this blog, we'll show you how EAM software could turn your maintenance strategy into a competitive differentiator.
Here’s why getting ahead of maintenance matters.
Improved Uptime
Robust EAM software provides your maintenance department with the tools they need to meet their standards for equipment uptime, asset longevity and safety—while controlling costs. This leads to a marked improvement in uptime. To meet production goals, get shipments out on time and fulfill sales orders, your organization needs all equipment to operate properly.
But if you don’t have a proactive maintenance plan in place, your maintenance team could be wasting as much as 20% of their day waiting for further instructions. With an EAM, you can not only do more with less, but you could cut the constant reactive maintenance scramble by over 65%.
EAM helps you increase the lifespan of your assets, because your team can stay on top of maintenance issues before they arise. In asset-intensive industries, like manufacturing, a reactive maintenance strategy is not sustainable if you want to grow. Fixing assets as they break leads to burgeoning downtime costs, reduced inventory and can often lead to safety issues for your team. In fact, according to a report by the Aberdeen Group, more than 80% of companies experience unplanned downtime every year, and a four-hour outage costs the average company a staggering $2 million.
Improved Performance and Longevity
If your company regularly experiences unplanned downtime, it could cost you dearly. In the same Aberdeen study, they found that almost 50% of companies couldn’t deliver their products to customers due to downtime, and another 37% lost production time due to failure of a critical asset. Because an EAM helps your company move from a reactive maintenance strategy to a predictive one, users will experience an immediate upsurge in productivity, while simultaneously reducing equipment downtime and failures. Think how much money you could save if you even reduced that by half.
EAM software collects vast amounts of data on your assets providing your plant operations team a detailed view of how your assets are performing. This ensures that they will keep running at full capacity for as long as possible. EAM helps you manage the details of maintenance, which helps you reduce “turn time” for shutdowns or minimize stoppages due to part stockouts or labor shortages. Your assets will perform better, because they will always get the right care at the right time. And when an asset nears the end of its functional life, your EAM can help you decide when to repair and when to replace it.
Improved Visibility
A robust EAM system eliminates departmental information silos and facilitates communication and collaboration throughout your enterprise. For example, if someone pulls one part from inventory for a work order, the inventory is automatically updated. Your EAM should give you a 360-degree view of the current condition and location of all your assets, even across multiple sites. The solution constantly monitors asset condition and performance and compiles historical data. This helps you spot issues and anomalies.
Then, the system analyzes these patterns and gives you workable analytics to help you tackle potential problems before they arise. It also gives you the hard data you need to schedule maintenance repairs with precision. You can also tailor reports to which Key Performance Indicators (KPIs) you want to measure, which will give you the best indicators of where and when to use your maintenance budget. If you are striving for plant operations excellence, you’ll need to follow a pattern of continuous quality improvement.
Let’s say you want to examine how quickly priority work orders are addressed. The data contained in your EAM platform can give you historical data on work order response times. Then management can use that data to try out new and improved workflows or processes and hold technicians accountable for following them. Built-in Business Intelligence (BI) even lets you test out various scenarios to see which would work best to improve your current maintenance strategy.
Why EAM?
If you have enterprise assets and equipment that needs to be tracked, or if you have assets across multiple departments and need to streamline processes and improve communications, then EAM is for you. If you have hundreds of physical assets, along with complex systems and operations across multiple sites, and you need better asset and inventory management to reduce costs, EAM is a necessity. If you’d like to make your asset strategy proactive, then you need an EAM.
Enterprise asset management can lower asset-related operating costs, extend the life span of an asset and improve visibility across your enterprise. If you’re still not sure, Aptean’s EAM comes with CMMS already built in, which is ideal for smaller manufacturing operations that still need to automate their manual maintenance processes. It’s a fast-moving industry—and if you don’t have the right technology, you’ll fall behind.
Aptean’s EAM software gives manufacturers all the tools you need to maximize asset performance, control maintenance costs and improve operational efficiency. Find out how, now.
Ready to start transforming your business?
We’ve got the specialized EAM solutions you need to conquer your industry challenges.
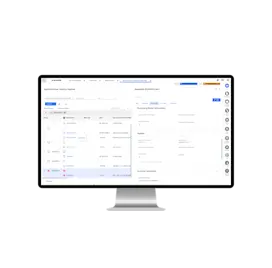