Meet Objective from Aptean—Injection Molding Software
Meet Objective from Aptean—Injection Molding Software
Meet Objective from Aptean—Injection Molding Software
14 Juli 2022
Toni Guillen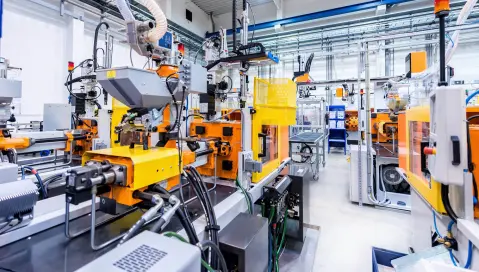
Producers know that in injection molding manufacturing, productivity is profit.
Particularly if you're manufacturing large quantities of low-priced goods. Thermoformed pots for agricultural use, single-use plastics for the healthcare sector or recycled plastic bottles for the beauty industry—they're all vital products, but producing them is a delicate balance of cost and efficiency.
Your clients are very discerning, so the quality of these items must be tip-top—and their quantity must be exact every time. Accuracy is paramount. What's more, the goods may be cheap, but the manufacturing equipment is certainly not. Being able to think and move fast in this sector is what separates the best producers from the rest.
The Need for Speed, Quality and Accuracy
We at Objective from Aptean understand that producers are hyper-focused on quality before production starts. If the process isn't perfect from the word go, the destroyed product and wasted time can cost you dearly.
Every single item, every pot and bottle, counts. Your software should be able to track every single product you make—right from receipt of raw materials, to delivery to your customer—or gate-to-gate, as we call it.
A strong manufacturing execution system (MES) is vital for production. Ideally, it will optimize efficiency in both your machines and your people, build as much automation into your processes as possible to remove human error and not only deliver useful KPIs and reports, but help you use them practically to boost your business.
Meanwhile, on the logistics side, a good warehouse management system (WMS) is vital to track all movements of stock, going from reception to production, production to your customers and everywhere in-between.
The ideal is getting one system that can do both, and that's what Objective from Aptean provides—a unique integrated MES & WMS solution, that tracks all movements and processes to and from your factory and on the shop floor.
It can calculate numerous KPIs that it then uses to make your business more efficient, including on yield, rework, cycle times, overall equipment effectiveness (OEE), causes of machine stoppages, material consumption and performance of operators.
Its major benefit—besides ultimate efficiency—is full lot traceability across your products. That means minimum waste, maximum profit, maximum speed and keeping your customers happy.
Real-Time Lot Traceability and Analysis
Lot traceability allows you to fully track your products along the supply chain offering complete visibility and transparency—and this applies to every single order.
If you have to issue a product recall, for example, you can use Objective from Aptean's MES and WMS to drill down into the data and find the root cause, wherever it is in your supply chain.
The systems also give you an unbeatably accurate picture of your stock, so you know exactly what materials you have, which makes your ordering process more accurate and efficient.
They also allow you to see which of your products are performing best. Are your fast movers actually moving as fast as you think?
Planning Your Production
Our intelligent MES can help you plan your production either manually or automatically. It uses algorithms in conjunction with both KPIs and data on available machines, resources and people to generate a planning proposal.
Once you've approved the proposal, operation can start automatically and you can monitor progress in real time, including supervision and management of your production department.
Our MES's easy-to-understand dashboards give you helpful visualizations of your relevant production data, and the system automatically generates reports on malfunctions, interruptions and quality data.
Shop Floor Efficiency
Objective from Aptean can speed your business up—literally.
Our WMS can plan out physical movements on the shop floor, making them as efficient as possible, with fewer empty movements. That ensures there's a pallet on the forks of a truck as often as there can be, and that the right materials are arriving at the line, every time.
Writing Your Own Rules
A lot of flexibility is required in the modern factory and warehouse—a lot of product variations, such as bio or kosher, require different types of quality checks that need to be done during production.
A big part of Objective from Aptean's popularity stems from its high configurability. Our customers can set their own rules from within the system, with no skills needed in programming.
For example, a food manufacturer may need to store certain products in a different location because of allergens. Typically, in MES and WMS systems, you would need those rules to be scripted, and it may cost you more money, as well as time, to go back to your implementation partner to change those rules.
At Objective from Aptean, we have focused heavily on our graphical user interface (GUI), allowing our customers to configure the rules themselves with a few simple actions on the platform.
Customer Specifications: Less Room for Error
We find that more manufacturers are moving from build-to-print (providing capacity for molding) towards build-to-spec—where the molding company designs the product based on functional specifications.
Molding companies are being asked to specify and design the products of the future, and customers are making increasingly stringent demands—on quality assurance, on delivery times, on lot traceability, on liability and on production hygiene.
All these demands are proving expensive for manufacturers. Added investment in machinery and IT means costs must be kept as affordable as possible, and there is little room for error.
Objective from Aptean's system combines both MES and WMS in one system to take the entire process out of human hands to minimize risk of costly mistakes.
As an example, one of our clients manufactures a pump used in heart surgery which requires vitally important quality checks on the grain of the plastic used, including its elasticity and the temperature at which it melts. Getting these checks wrong could have catastrophic consequences, especially if lot traceability isn't being used.
Checks can be automated based on master data, removing the risk of human error from the operator.
Innovate via Efficiency
Injection molding technology is mature, but there is still innovation in the field. Higher speeds, lower changeover times, more flexibility, lower energy and raw material consumption, and big data management—these are what will help you drive your business forward, and Objective from Aptean's combined MES & WMS is designed to do it.
The value lies in the fact that it's one system. The WMS and MES sides work together seamlessly, so you can oversee the logistics and production sides of your business as one.
There's something else that makes Objective from Aptean different. Our senior manager professional services, Tom Matthijs, says, “We are hyper-focused on production and logistics. We don't build machines and then build software to work that machine—we specialize in the software. We build software that can work with all your machines. That means we are able to move as fast with our customers as they require.”
Objective has long been a trusted name in the injection molding industry, and Aptean, which acquired the business in 2021, has the expertise and resources to help customers achieve optimal results.
In the modern factory, there's no reason why you can't turn your reams of data into useful, actionable KPIs and then squeeze every ounce of efficiency from your business.
Ready to learn more about Objective from Aptean and how it can boost your molding business’s performance? Contact us today, or schedule a personalized demo.
Related Content
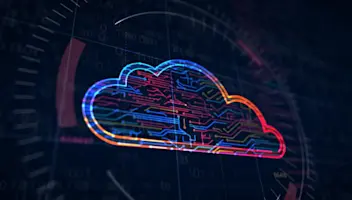
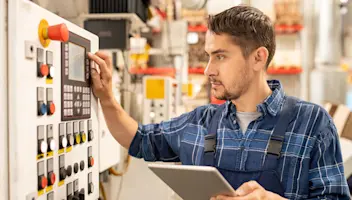
Sind Sie bereit, Ihr Unternehmen grundlegend zu verändern?
Wir bieten Ihnen die spezialisierte MES-Lösung, die Sie für die Herausforderungen Ihrer Branche benötigen.
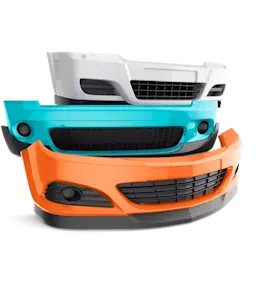